Kaizen Meaning: A Continuous Improvement Journey
Kaizen is a Japanese term that means “continuous improvement.” It has been around for over 100 years and can be applied to many aspects of life, including business. The meaning of Kaizen is all about making small changes and improvements in your daily work habits to create big results.
What is the Kaizen philosophy? (Kaizen Meaning)
Kaizen is a Japanese word that means “improvement” or “change for the better.” The philosophy of Kaizen has been adopted by many companies in Japan as well as other parts of the world with great success because it’s about continuous improvement rather than radical change.
Kaizen can be applied to anything – from business processes or personal habits! It’s the idea of making incremental improvements all the time in order to create something much better than it was before.
It might seem like Kaizen requires tons of work, but in reality Kaizen prioritises change for the better and can be implemented with minimal disruption.
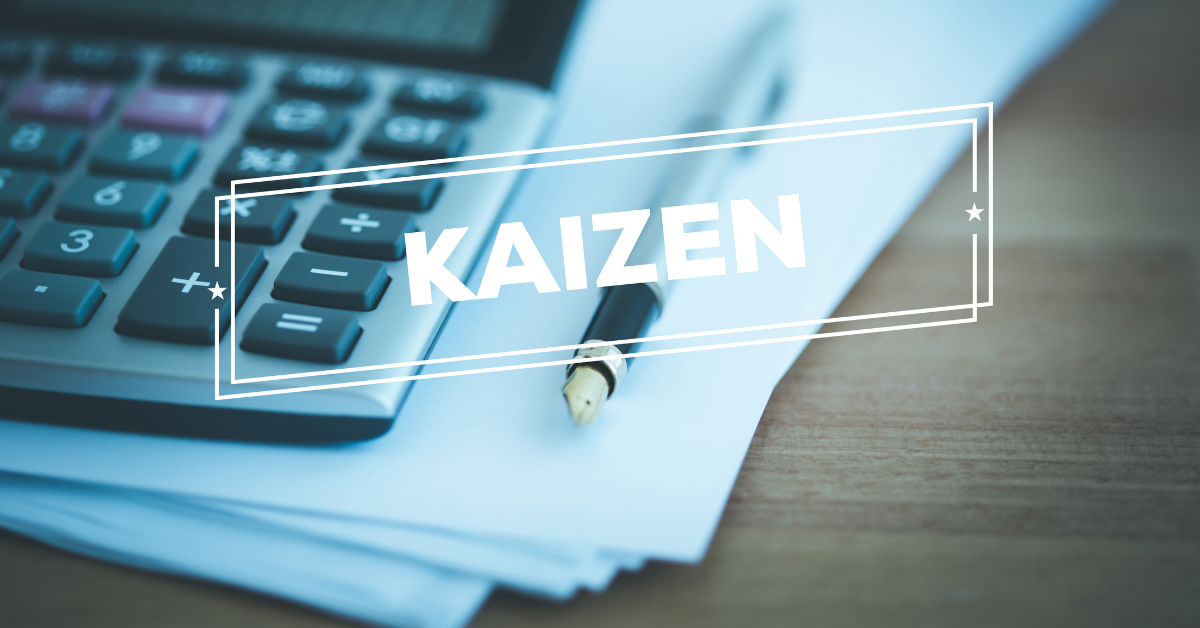
Even small changes can have huge impacts! Another way of looking at Kaizen is the process of making improvements in a disciplined, systematic way to improve quality and productivity while removing waste (Muda).
Interesting Read: Six Sigma Explained – Five Stages to Optimise Your Business
Kaizen method: Continuous improvement means incremental steps forward, not leaps. When you take continuous Kaizen actions, your team has a more structured mindset and method, where small improvements add up to something big.
When you need a change, it is best to start small and then build from there. This way the changes are more manageable for both employees and managers alike.
What is the purpose of Kaizen?
In a Kaizen event there are always two phases: an ideation phase and a quick implementation phase where action items are generated with consensus from the whole team. This method is part of a Japanese culture that was originally developed to improve the production processes.
To build competitive success, Kaizen is a way to improve processes, products and services. As a part of management strategy, the purpose of improvement in Kaizen method is to make the workplace more efficient, with a goal of increasing productivity and quality.
Interesting Read: What is operations management? What you need to know
Management strategy that implements the best practices of the method experience process improvement in decision making, problem solving, group communication, and teamwork.
As such, this method can be applied to any company that is interested in efficiency and success. It is a process that leads to increased productivity and quality which can lead to economic growth of an organisation.
What are the principles of Kaizen?
The Kaizen philosophy relies on these key principles – Plan ahead, be open-minded, and focus on what needs fixing first.
Know Your Customer
One of the most important ways to ensure that your product or service is sold effectively and appreciated by those who receive it, you must know who they are. By identifying their interests and enhancing their experience through knowledge about what they want from the interaction with you company, one can better deliver on need – whether explicit or implicit.
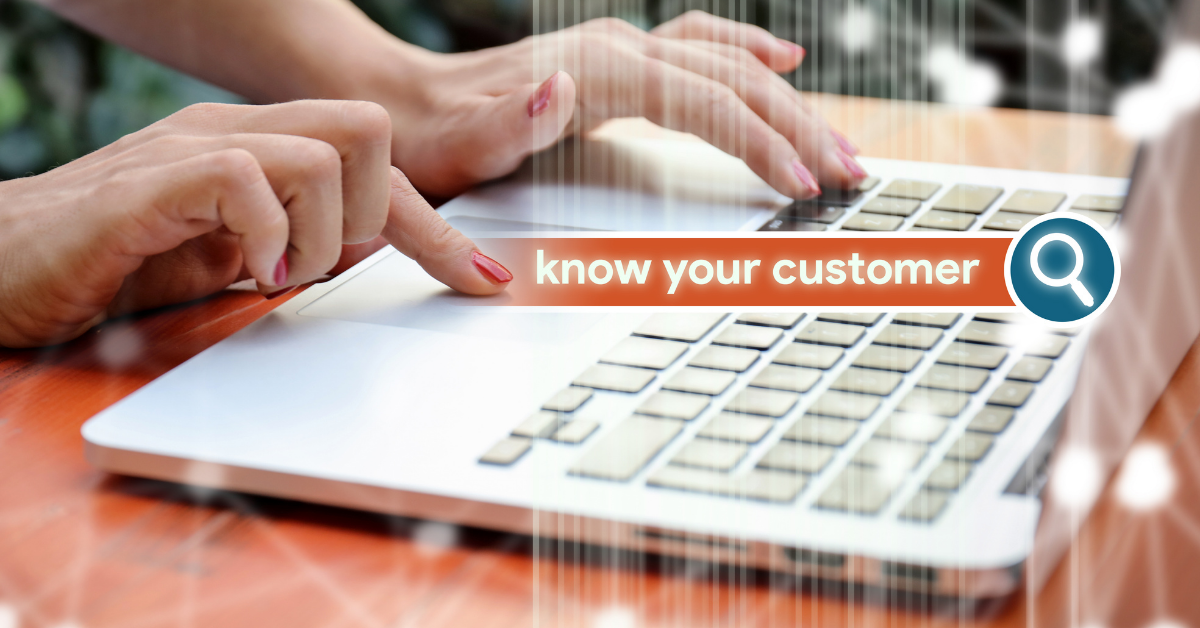
Most importantly in order for a customer’s needs to be met-whether explicitly expressed when purchasing but also implicitly felt afterward-it is key to identify them first so as not only meet expectations but exceed them.
Let it Flow
On the hunt for zero waste, everyone is working towards removing any and all wasted products from their business. It might be an impossible goal but that’s what Kaizen meaning is: if you could achieve it then improvement would stop.
This applies to the target of eliminating every last bit of wasted product while also creating value at work – which can’t happen without these innovative changes being made everywhere.
Empower People
This one is directed towards teams and having them organised in such a way that it supports the Kaizen principles. Therefore, by setting goals for their team members not contradictory to each other with systems and tools offered from leadership, they can make sure everyone’s on board.
Interesting Read: The Keys to Strategic Management for Business Process Outsourcing Firms
Improvement Kaizen involves the concept of managing people, processes and tools for the purpose of constantly improving.

To do that effectively, you need to have a team who agrees with what they’re trying to accomplish and understands how they can play their part in achieving it. You also need a system to ensure that everyone on the team is working towards getting better together!
Be Transparent
In this day and age, data is king. It’s the metric that measures success in a number of different fields. In order to improve performance and stay on top, you need to track it with real numbers!
Transparency and data-tracking are important for making improvements.
If you have a problem in your process, it’s going to be hard to diagnose and fix if no one knows about it! Data can help identify what the problems are before they become too big of an issue.
Eliminate Waste
Kaizen is a Japanese philosophy that analyzes and removes waste, or “muda”. Mura means to identify imbalances in the system caused by inconsistencies of people’s workflows within an organisation; Muri refers to doing something beyond what one can do without jeopardising health or safety. By following Kaizen principles like these three MU-s: muda (waste), mura (imbalance) and muri (exhaustion), companies will be able to thrive!
Now that you know the Kaizen meaning…
The concept of Kaizen is fundamentally simple. It’s the idea that you can continuously improve your business practices, even if it seems like an impossible task at first.
These are all ideas you can put into practice to improve your business practices and see an increase in productivity, efficiency, and quality. What is one thing you’re going to apply from this post?
Are you tired of…Messy, manual processes that can't be scaled?
We work with operations leaders looking to digitally transform their manual back-office processes and procedures.
We combine your existing business processes with our software, plus decades of enterprise process re-engineering and change management experience to quickly scale and see the results you are looking for.