The Top 3 Operations Bottlenecks That You Need to Pay Attention to
Have you ever thought about bottlenecks in your operations? If not, don’t worry! You’re not alone. But bottlenecks can be a major problem for many companies.
This is because they affect the flow of work and can lead to issues downstream as well. In this blog post we will take a look at the top 3 bottlenecks that occur in operations and how you can optimise them so that they become bottleneck-free zones!
What are bottlenecks and why are they bad?
A bottleneck occurs when the work has to go through a single point. This slows down production and limits capacity by creating bottlenecks downstream as well.
For example, in manufacturing plants bottlenecks occur at machines or conveyors because they cannot be used simultaneously without slowing down productivity.
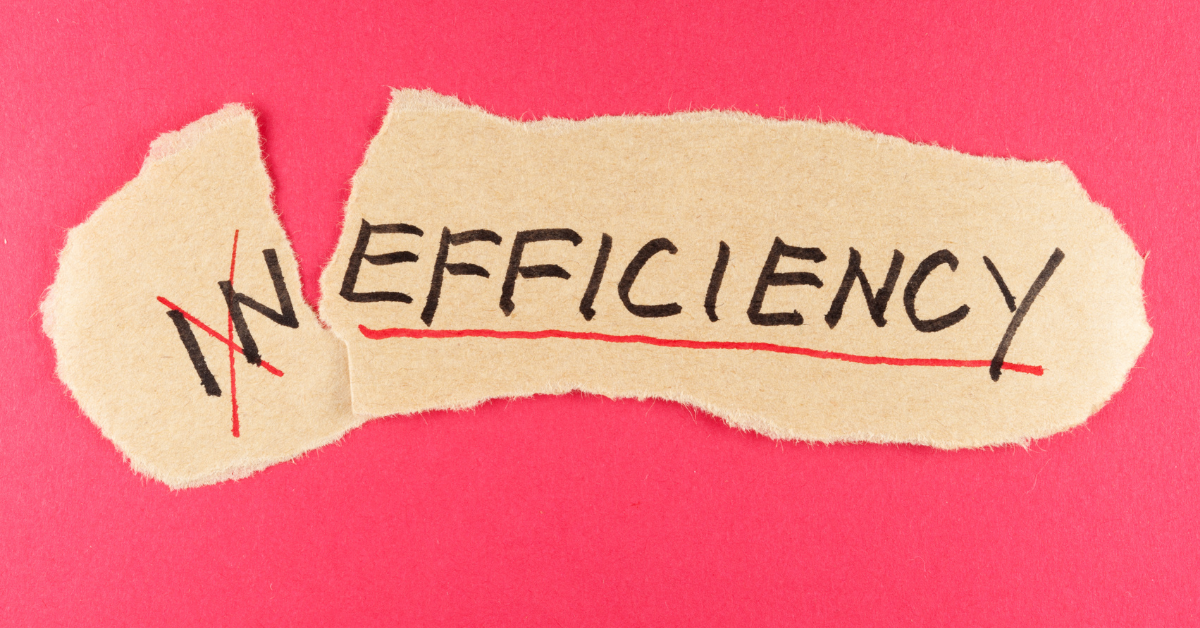
We’re not here today just to talk about the manufacturing industry, as bottlenecks occur in service-based industries as well.
Bottlenecks in operations disrupt the workflow and make it difficult to meet deadlines. It exhaust companies’ resources and assets, and in the end, it results in lost revenue.
How to Identify Them
It is important to practice the art of identifying bottlenecks so that your team can prepare a strategy before they become a problem.
The bottlenecks are the points in your operations where you feel like you’re fighting against time and/or people to get things done. Figure out which process is slowing down or causing problems by looking at the data from each step of your operation.
Interesting Read: Kaizen Meaning – A Continuous Improvement
The way to do this is to make a timeline that includes all of the bottlenecks in your operations.
Here are some signs that you have bottlenecks in your business process:
Long wait times
Long wait times are one of the most frustrating things for customers. Waiting on a product, report or more information can delay your work and cause you to feel like time is passing slower than usual.
Material waiting between steps in processes also leads to delays that may not be obvious at first glance but when coupled with other factors create bottlenecks later down the line.
These long wait times cause a lot of problems. For example, your work is delayed because you’re waiting for product information or more data. Materials also spend time while they are in the middle of business processes as well.
Backlogged work
The backlog is a never-ending tale of being overwhelmed with work. There’s too much piled up and not enough resources to go around, forcing you into an endless cycle of getting nowhere fast.
It’s impossible to get ahead of the backlog. And because bottlenecks typically happen when you’re waiting for product information or more data, sometimes a bottleneck will cause bottlenecks in other areas that may not be obvious at first glance but when coupled with bottlenecks from other factors create bottlenecks later.
High stress levels
When people are unable to find a solution or the right answer, it can cause them anxiety. Especially when they know that their inability is holding up others and this makes for high stress levels.
When someone feels like time is running out, they may become overwhelmed with anxious thoughts about what might happen if nothing changes soon enough.
3 Operations Bottlenecks to Watch Out For
Here are some of the top operations bottlenecks that businesses must watch out for:

1. Too Long to Complete
Processes take too long to complete, which slows down production or service delivery downstream. This can include tasks such as processing a customer’s order; approval of transactions for payment approvals and deposits; details about employees like their work hours.
Interesting Read: Six Sigma Explained – Five Stages to Optimise Your Business
This bottleneck might be a result of bottlenecks in other parts of the process, such as bottlenecks created by a lack of capacity for tasks like processing transactions. It might be related to the availability of resources, or even inconsistent standards in your management system.
2. Human Error
Processes are done incorrectly due to human error (e.g., sending an email or entering data into Excel). This bottleneck might be a result of an inconsistent or bad onboarding processes, or simply a lack of capacity for the task. These sorts of bottlenecks can be solved by having processes, training activities and tools that are easy to use, understand and adopt.
Having a better workflow for your new employee training is also key. This bottlenecks will disappear after new employees have been through the on-boarding process, and they are more aware of their role in your business.
3. Awaiting Approval from Higher-Ups
Processes cannot move forward because they’re awaiting approval from higher-ups (e.g., someone with visibility into operations at headquarters). You might need to restructure the way you run your business so that your business process don’t just rely on one person.

Instead of slowing down the process, you can set up a system in your company that will help speed up the approval process such as a clear benchmark of what is needed to get the approval.
Ideally bottlenecks should be addressed as soon they are noticed. This will help to ensure that any bottlenecks observed during a regular review of operations don’t get worse over time and can be resolved quickly, without impacting the organisation’s processes or timelines for achieving goals.
Are you tired of…Messy, manual processes that can't be scaled?
We work with operations leaders looking to digitally transform their manual back-office processes and procedures.
We combine your existing business processes with our software, plus decades of enterprise process re-engineering and change management experience to quickly scale and see the results you are looking for.