Effective Operations Management with Value Stream Mapping (VSM)
Value Stream Mapping (VSM) is a lean manufacturing technique that can be applied to any operations management.
VSM focuses on improving the process of how value flows from raw material to the customer by eliminating waste or excess work-in-progress inventory.
It also helps identify areas for improvement and create a better understanding of the operations and processes within your company.
In this blog, we’ll discuss what Value Stream Mapping is, why it’s important for operations management, and some best practices that will help you get started with VSM in your own company!
What is Value Stream Mapping (VSM)
Before we go too deep into operations management and Value Stream Mapping (VSM), it’s important to first understand what it is.
In operations and logistics, a Value Stream Map or flowchart can be used for visualising the path that input materials take until they are transformed into an output product. A company may also have operations management and value stream mapping in its manufacturing processes.
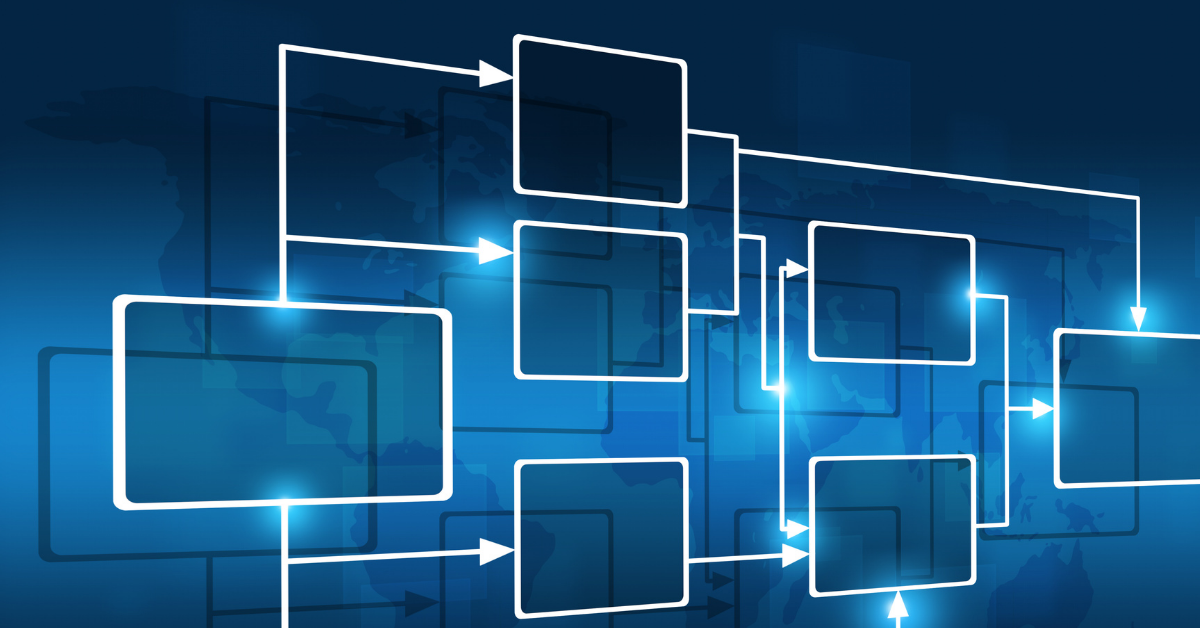
A VSM can help operations managers see the whole process at a glance, identify bottlenecks, or other points of delay, as well as note opportunities for optimisation.
For example: if one step in the production line is taking significantly longer than any others then operations management will need to analyse the material and information flow to identify the cause of this (perhaps it is inefficiently performing operations or there are too many steps).
It may then take corrective action such as adjusting operations, re-designing a process or eliminating unnecessary steps.
Furthermore, operations management can use VSM to see how changes in one part will affect other parts downstream and so reduce lead time and improve the overall business operations efficiency.
VSM Application to Operations Management
You might have heard a lot of other Lean methodology terms in operations management before. For example, Six Sigma, Kaizen Burst, Kanban Board, or others! Value stream mapping is one of those things that are not always well understood because it has a rather complex definition.
For more on Kanban, how to get started and to find out the secret of how Fortune 500 companies reach operational excellence check out the Process Optimisation Blueprint:
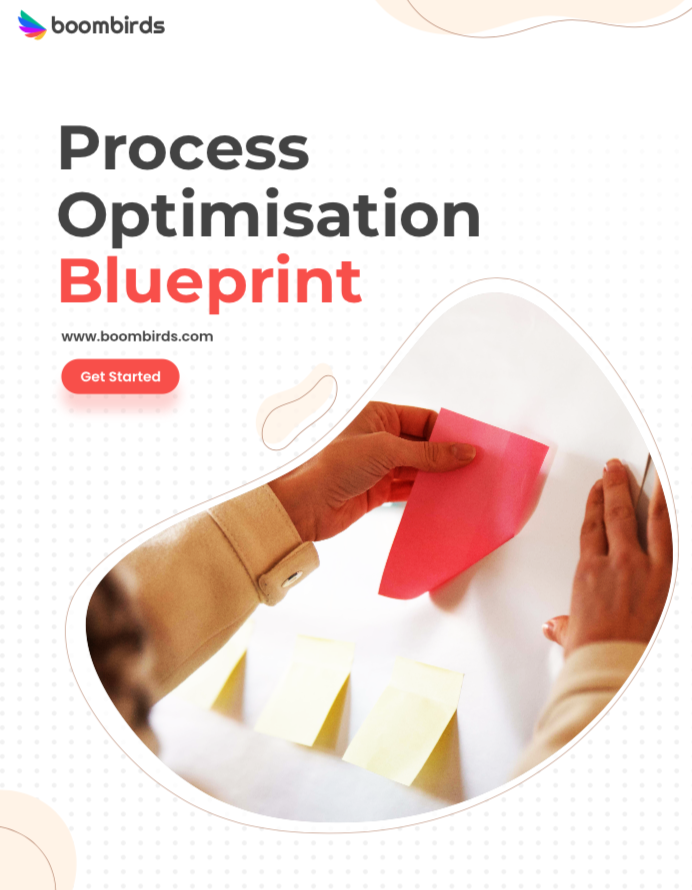
A VSM helps identify opportunities for operational improvements by showing the steps from raw material to finished product or service with all associated costs identified at each step.
As we have already established, the most efficient way to reduce inefficiencies is not by focusing on individual processes. The best approach should be looking across your entire value stream for all potential sources of problems and then identifying how you can solve them!
Management can use value stream mapping to identify the inherent waste and losses within an operation. This helps them find ways to optimise their operations with respect to costs, resources, etc.
Benefits of value stream mapping for operations management
As a management tool, Value Stream Mapping (VSM) is used to:
Visualise Current State Map
Value Stream Mapping allows you to not only visualise the tasks that are performed. But also how information is transmitted and materials flow throughout all of an organisation’s processes.
This can lead to some powerful insights about inefficiencies as well as opportunities for improvement.
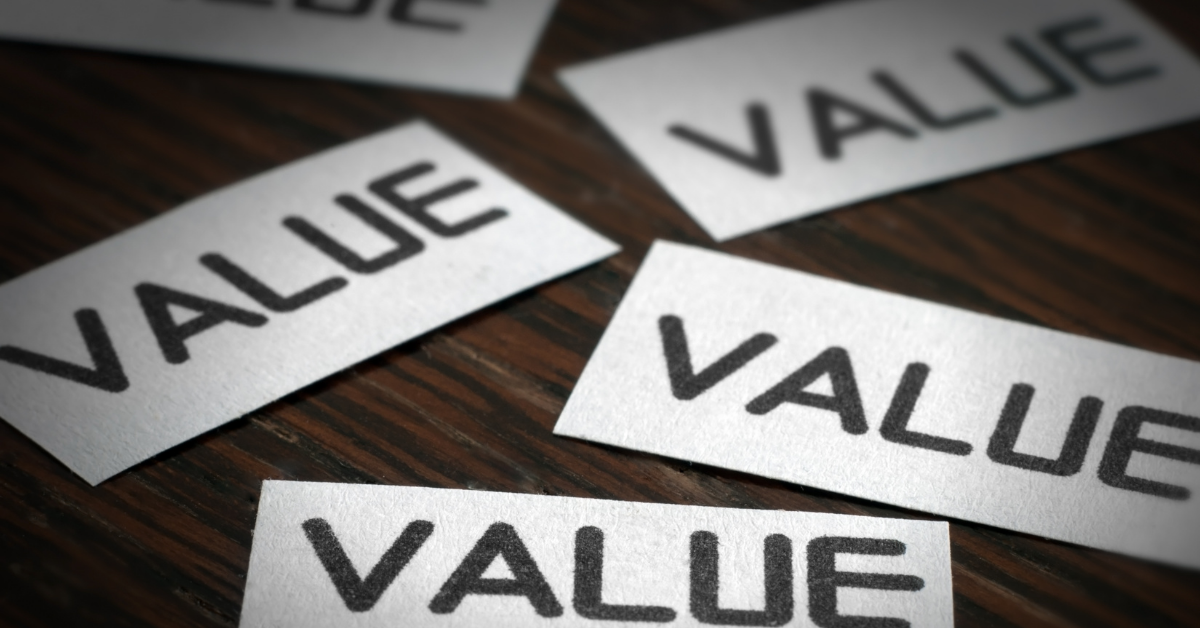
Visualising and analysing your current state assists you in re-engineering your future state so that you can focus on developing value adding activities.
Value stream maps are the paths that materials follow throughout operations and logistics from supplier to customer, or through a series of operations in the supply chain.
Identify Areas for Process Improvement
A complex system can be difficult to understand and analyse. A Value Stream Map is not your average visualisation method because it includes the flow of material, resource information, input tasks for a process or any other factors necessary in order to create an efficient production line. And with that much data incorporated into a simple, and graphical, representation on paper you’re able to identify problems quickly and easily!
One of the keys to effective operations management is breaking down all operations into smaller pieces or sub-processes that can be analysed individually, holistically and objectively. Mapping the value stream helps to achieve this by illustrating a complex process in its entirety with information.
Identifying the non value activities in your current state value stream is the first step to operations management. You can then create a plan for executing these tasks or processes more effectively and efficiently by re-designing them with value in mind.
Guide Development Process for Your Team Members
In order to make a difference in their organisation, managers are going to have to focus on changing the culture. That change can only be accomplished by making sure that all stakeholders understand what needs they should fill and how those efforts will help them achieve success.
This is why we develop countermeasures in highly visual ways that allow for easy understanding of problem areas so as not just implement our own strategies but also get others involved with theirs too!
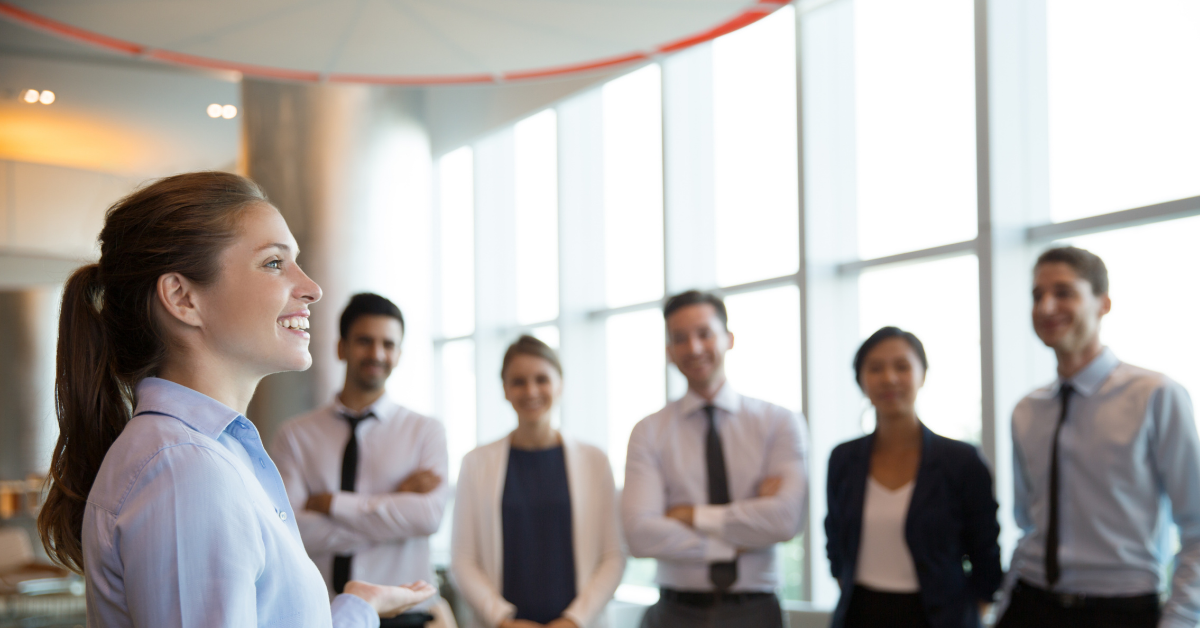
The entire Value Stream Mapping process uses graphical depictions of limiting factors which any stakeholder can easily visualise because these illustrations show more than words, solely, ever could.
Not only does this facilitate effective communication between different departments it motivates everyone involved through active involvement at every stage throughout the process
The Basics of VSM Process Mapping Notation
A Value Stream Map is a special type of flowchart that focuses exclusively on the successful flow of product materials. The VSM breaks down different steps and provides information related to that step based on:
Time
Quantity
Quality
Other relevant metrics
Here are some key symbols that you can include in your value stream mapping exercise:
– Checkpoints: these are checkpoints that can be based on time or a specific quantity. These ensure the product successfully passed through this checkpoint and has been delivered to the next stage of operations management.
– Lines: A line is an operations process step, it’s where materials move from one station to the other.
– Stations: these are operations process steps that require more than one person or machine. These can include whatever need to be done in order for the product to move on from this step.
– Events: operations events will happen during a particular stage of operation management; they could range
-Two symbols represent flow direction
– Arrows are used to show the direction of operations flows and may be labeled on the diagram with a letter
There are actually many more key symbols that you can include in your state map to represent information flow, production system, and data.
But, for now let’s focus on the symbols that are needed to construct a basic operations flow chart.
The end-goal of creating a value stream is to create an ideal future state of materials and information flows, operations, and processes.
If you’re looking for a way to create lasting value and stop wasting time, then Lean might be the right choice for you.
Value Stream Mapping can help identify problems in your process so they can be solved!
It’s also intrinsically linked with Boombirds’ digital transformation platform. We do this by displaying a Value Stream Map view of all your critical processes, helping to identify potential bottlenecks and opportunities to continuous improvement. Find out more below.
Are you tired of…Messy, manual processes that can't be scaled?
We work with operations leaders looking to digitally transform their manual back-office processes and procedures.
We combine your existing business processes with our software, plus decades of enterprise process re-engineering and change management experience to quickly scale and see the results you are looking for.